How did our partner gain reliable installation protection despite unusual design conditions?
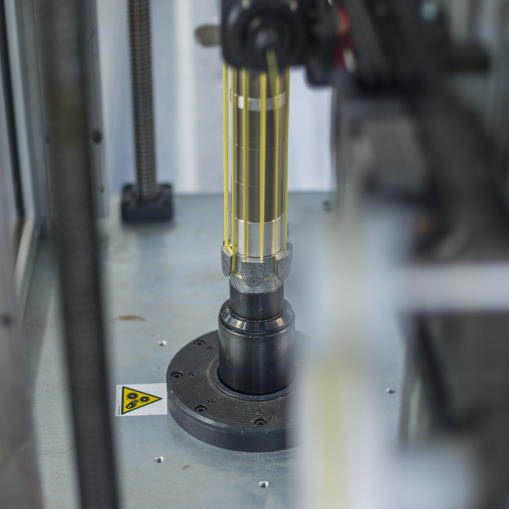
Before
Pursuing the idea of sustainable development, our Partner is expanding its photovoltaic farms and upgrading the in-house power grid. Due to these factors, the need for three additional medium-voltage switchgears arose:
- One for 30 kV to serve the photovoltaic farm. This switchgear was to be fed from the 110 kV GPZ and connected to the others via a 30 by 6 kV transformer,
- Two 6 kV rated switchgears for energy distribution and power supply to the plant.
Problem
These were the problems our partner was facing
Our partner needed surge protectors for all three new medium-voltage switchgear. Our tasks included the selection of surge arresters to protect the following MV equipment:
- switchboards,
- cable lines,
- transformers.
At the very beginning of our cooperation, we paid special attention to two hot spots specific to this project:
- transitions from cable lines to overhead lines and vice versa, that is, from overhead lines to cable lines. This is because surges of multiplied value can occur at these points. In addition, possible repairs of damage to cable lines require a lot of work and generate high costs. For these reasons, securing connections between cable lines and overhead lines requires special design care,
- incoming connection to transformers, which turned out to be overhead. Due to this fact, the last sections of the connection to the rest of the installation were made by means of an overhead line. Therefore, it was necessary to carefully calculate which set of surge arresters, installed at the end of the cable line, would effectively protect the MV transformer.
Another complication arose from the absence of an existing overvoltage protection design, necessitating us to undertake this task ourselves. Furthermore, during the design process, it became evident that not all the locations we identified met the technical requirements for installing the proposed surge arresters. This led to the need to select the parameters of these devices while also considering the unconventional installation locations.
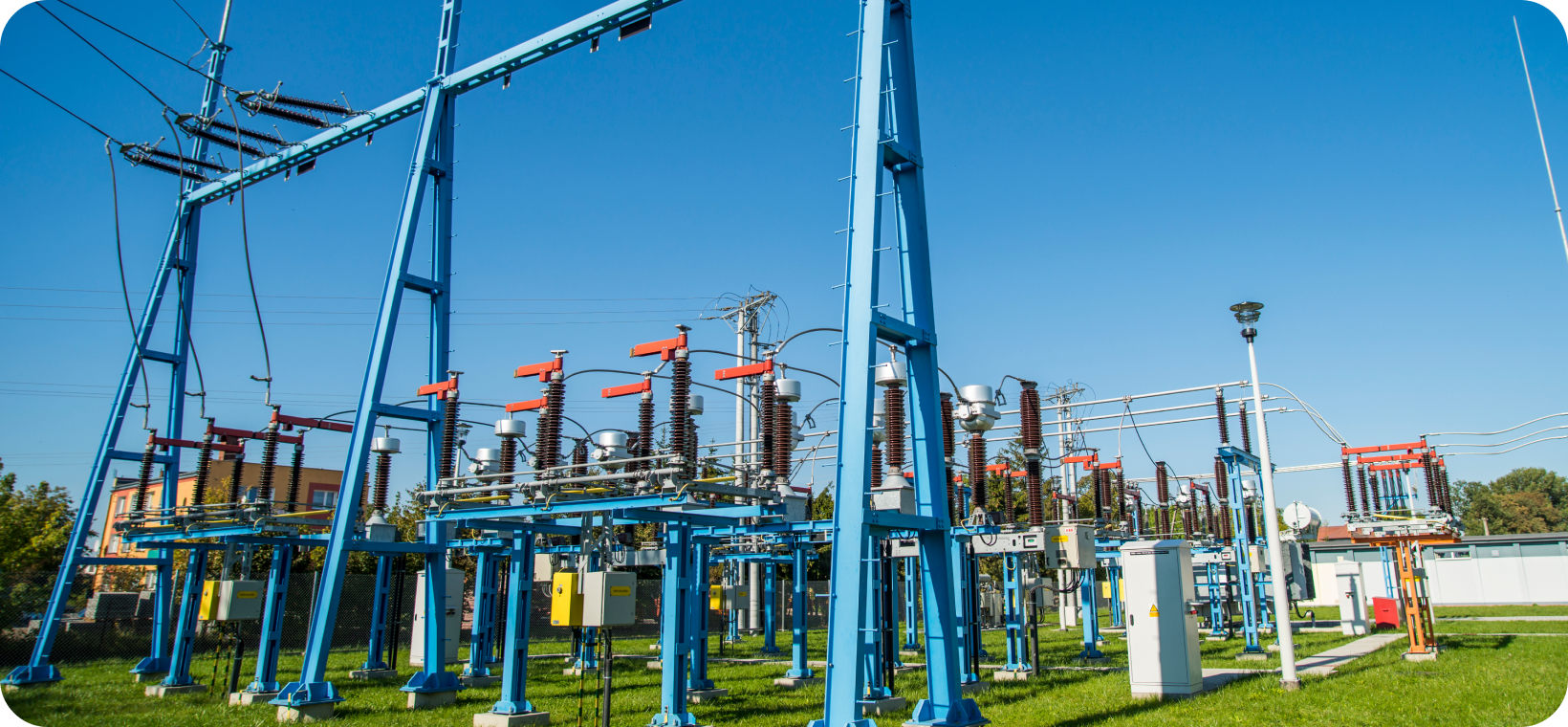
Solution
How did we solve the Partner’s problem?
To begin the work, it was crucial to receive the most comprehensive technical documentation of the existing electrical network from the Partner. This included photos of the facilities. In addition, we conducted two video conferences with employees of the client’s technical division. Although, as always, we were ready to come to the implementation site to perform a site visit, but in this case there was no need for that.
Our work consisted of:
- maximum operating voltage calculation of arresters,
- selection of models of our limiters,
- analyze the operating points behind and in front of the switches for the best location,
- delineation of protection zones, that is, determining how far the protection of individual sets of surge arresters extends,
- determining the working points, i.e. the installation locations due to the technical conditions available in the facility. We had to take into account the Partner’s requirements in the calculations, i.e. adjust the protective distance to them, and check whether this installation at the points proposed by the Partner would also protect what it was designed for,
- checking short-circuit conditions, i.e. checking short-circuit currents at the locations of the planned installation of surge arresters and, based on this, determining whether our solutions in the event of a failure will withstand the flow of short-circuit current according to the standard,
- manufacture and delivery of arresters with appropriate parameters,
- provision of technical documentation, and measurement results, i.e. approvals, installation and operation instructions, and product data sheets.
Although we had surge arresters in the catalog with parameters derived from our calculations, they were not mass-produced devices.
In this case, we made them from scratch, specifically for our Partner’s needs. Thus, we supplied the following types of surge arresters in the quantities specified:
PROXAR IIN 9.0 AC 1111010
3 pcs.
PROXAR IIN 24.0 AC 1111040
1 pcs.
PROXAR IIN 45 AC 1111060
3 pcs.
PROXAR IIW 45 AC 102210
9 pcs.
PROXAR IN 45 AC 112009
3 pcs.
The process, from the initial contact with our Partner to the submission of a comprehensive offer, took approximately 2 weeks. Subsequently, from the technical discussions conducted to the delivery of the appropriate surge arresters directly to the customer’s factory, the timeline spanned roughly 6 weeks. It’s worth noting that our Partner was obligated to follow a tender process, which extended our collaboration. However, it’s important to highlight on our side, that the implementation of this project proceeded faster than required by the Client.
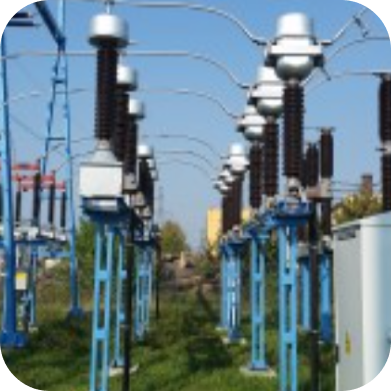
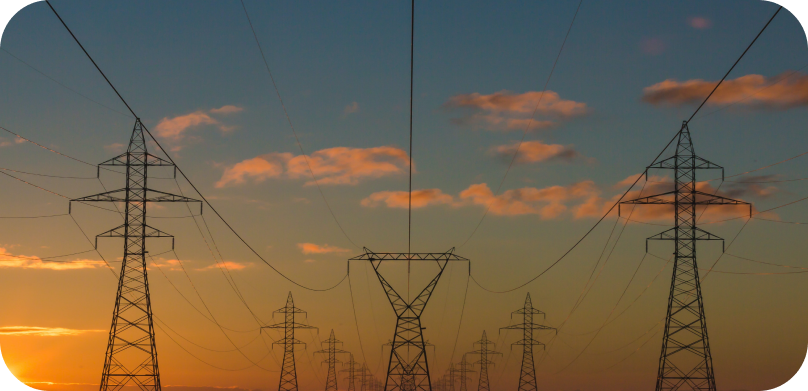
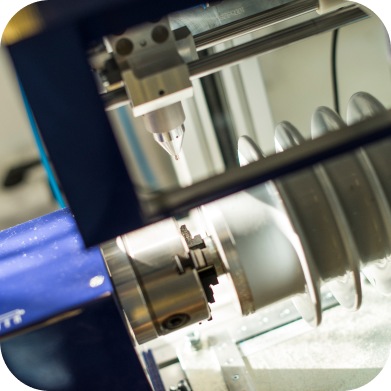
Effects
This is what the Partner gained from our cooperation
The work in this project was scheduled to be completed by the end of April 2023, but in mid-March some of the arresters were already installed and working properly under voltage. When the work was completed, the Partner acquired reliable protection for the installation supplying power to industrial plants. The number of surge damages was also expected to decrease. Regardless, our client has gained a trusted partner, which confirms the selection of Protektel as the supplier of replacement transformers in the next joint project.